VR-Based Equipment Learning Tool
Overview
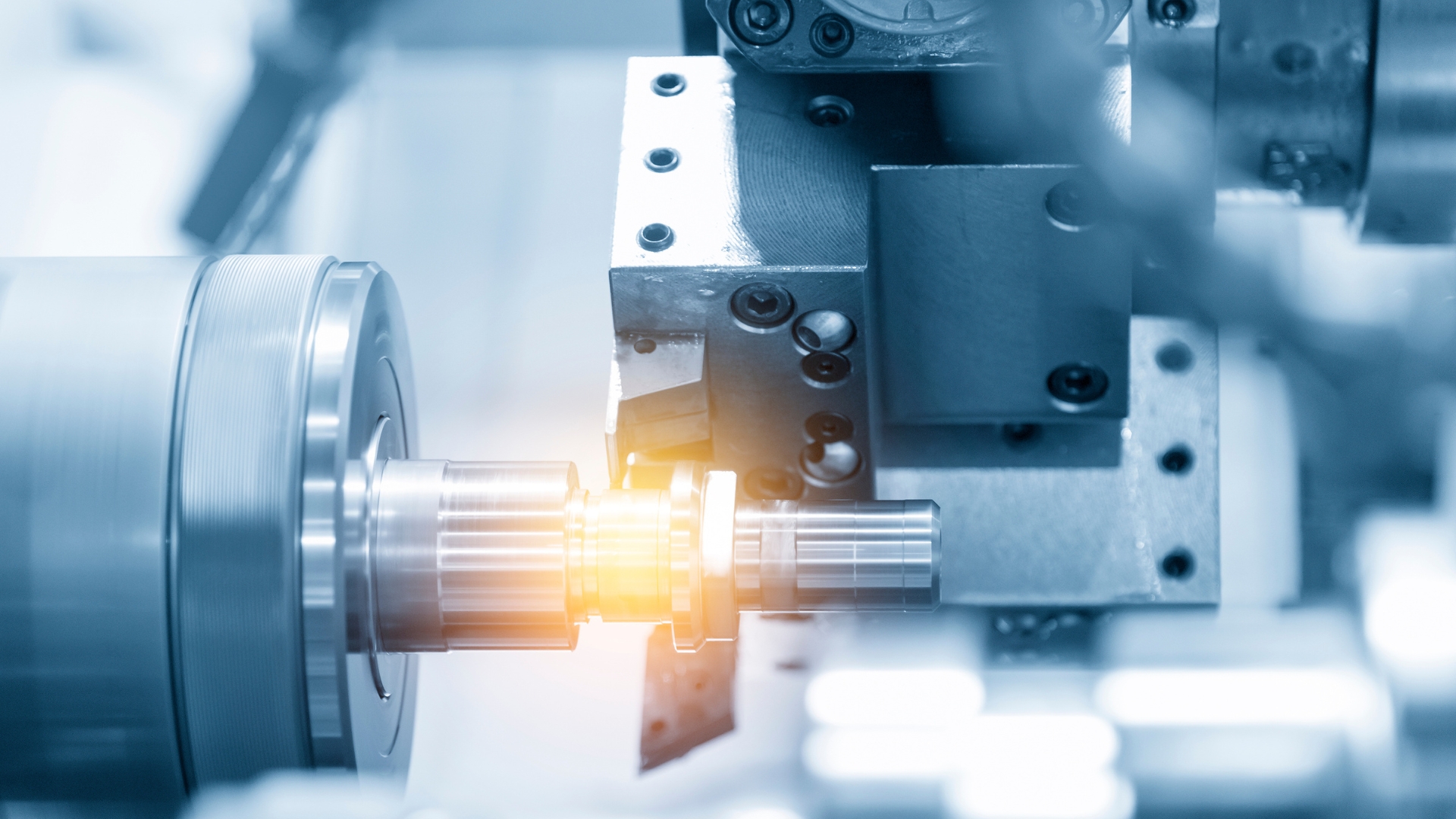
A lathe machine is a tool that rotates a workpiece on its axis to perform various operations such as cutting, drilling, facing, turning, knurling, and deformation. The machine uses various cutting tools to remove material from the workpiece and shape it into the desired form. Lathe machines can create a wide range of cylindrical, conical, and spherical shapes, threads, and other precision parts. They are widely used in manufacturing processes such as metalworking, woodworking, and glassworking, and can be operated manually or with computer-controlled automation.
Lathe machines have a long and rich history, dating back to ancient times when primitive versions were used to turn pottery and shape wood. Over time, these early lathes evolved and became more sophisticated, with metalworking lathes emerging during the Middle Ages. These early lathes were powered by hand or foot pedals and used primarily to turn cylindrical shapes such as bowls, cups, and furniture legs.
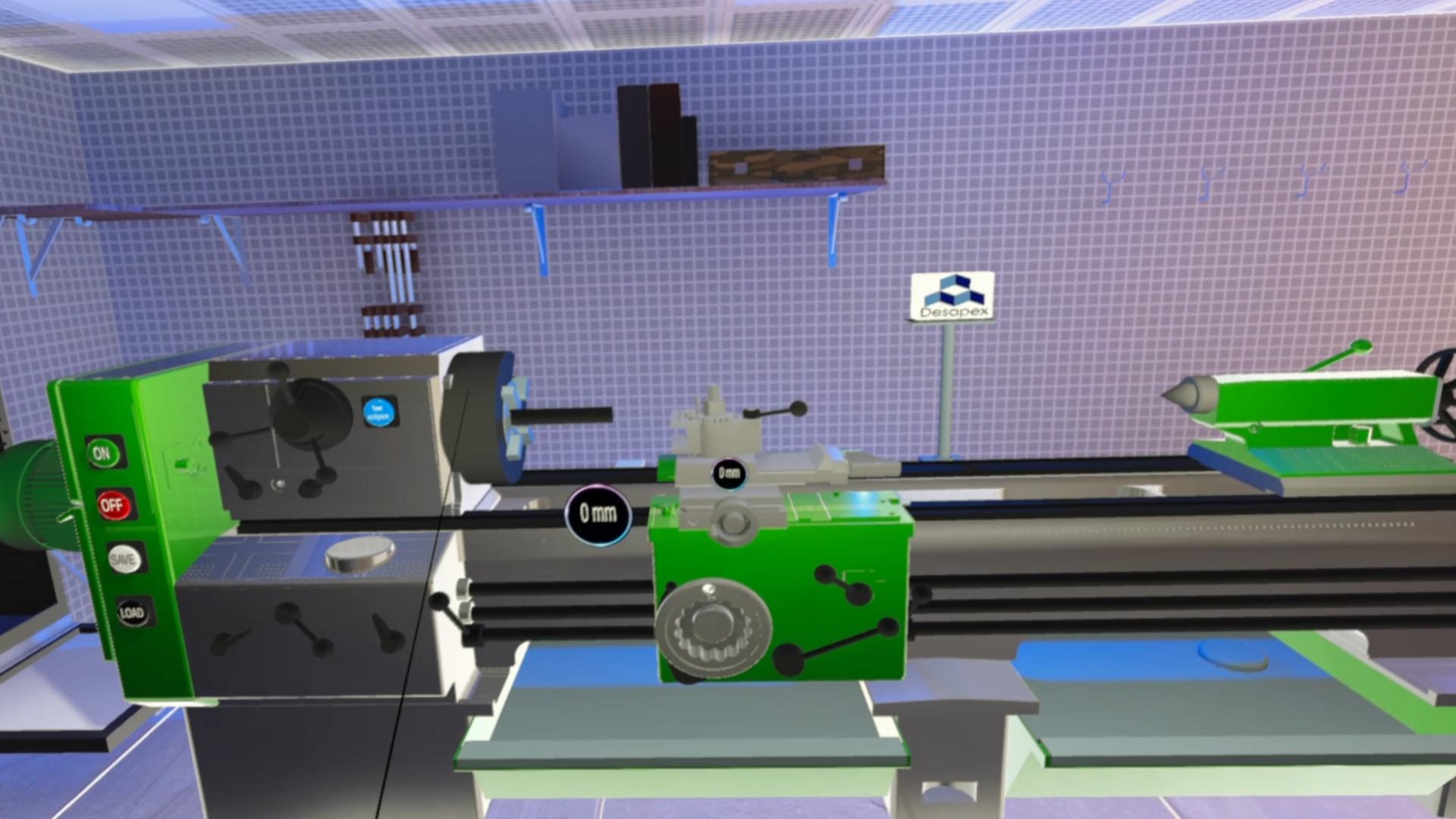
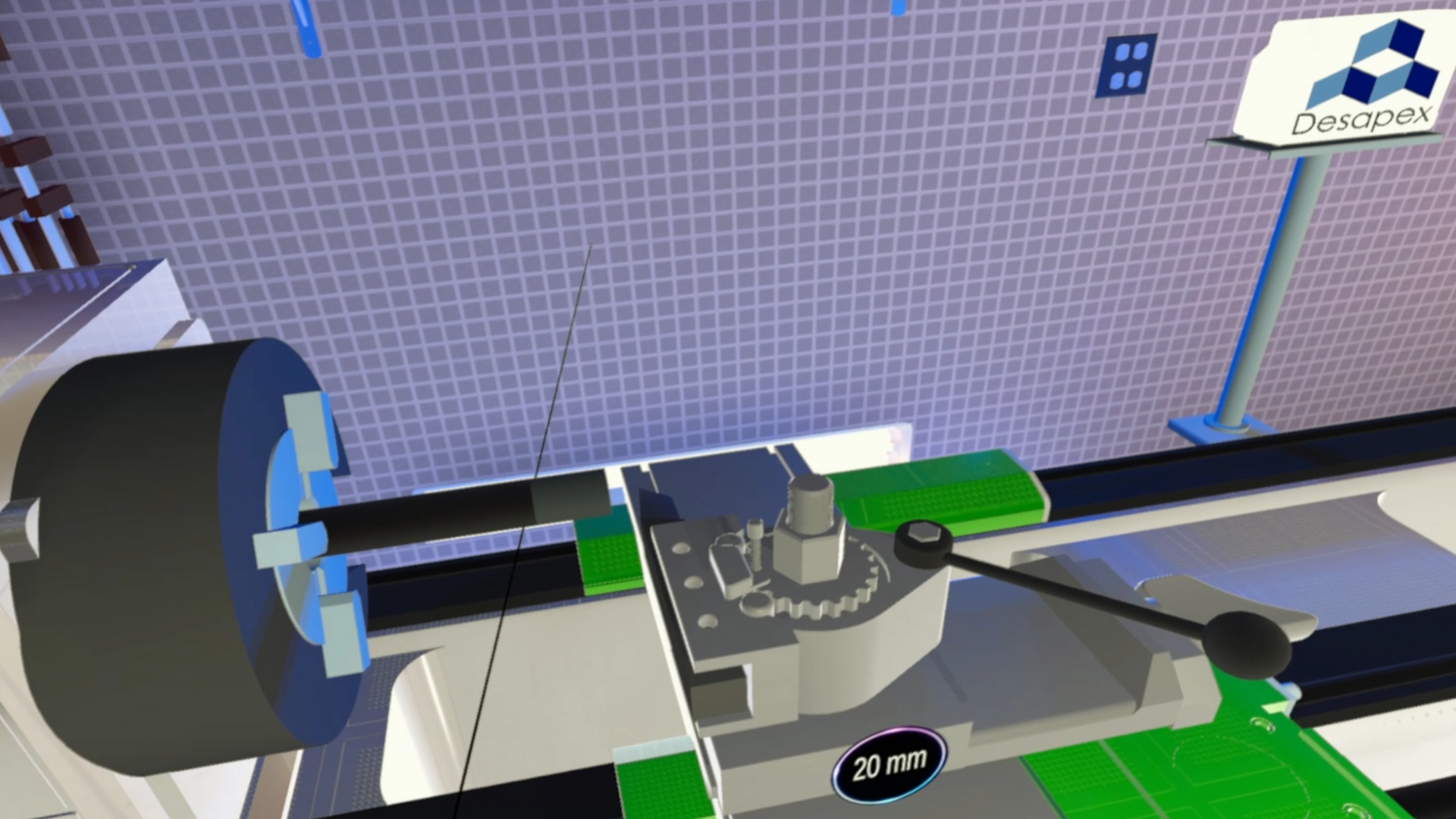
This blog depicts the features and uses of the VR-based lathe training tool. Virtual Reality (VR) based lathe training tools are computer programs that simulate the operation of a lathe machine in a virtual environment. These tools allow users to practice lathe machine operation and learn the necessary skills without using a physical machine, reducing the risk of accidents and damage to equipment.
The VR-based lathe training tool typically includes a virtual lathe machine that looks and functions like a real machine. Users wear a VR headset and use controllers to interact with the virtual machine. They can select and set tools, adjust the cutting speed, and perform various lathe operations, such as turning, drilling, and threading.
The training tool can provide instant feedback to users, showing them how their actions affect the machine and the material being worked on. This feedback allows users to learn from their mistakes and improve their skills.
Some VR-based lathe training tools also include interactive tutorials, demonstrations, and quizzes to help users learn the necessary concepts and techniques. These tools can be customized to match the specific lathe machine models and configurations used by a company or organization.
Through VR-based lathe training tools, testing the skills of operators can be done multiple times and the cost of training such as material cost can be erased. As VR provides the scope for making multiple trials, through this operators can enhance their skills in performing different lathe operations, benefitting towards minimizing capital and time.
Further, this blog provides all information on VR-based lathe training tools, their usage, value, and what all specialties VR training tools can offer to make complex things into simple solutions.
The Old Era Of Using Machinery & and Its Disadvantages
The old era of using machines, especially in the early days of the Industrial Revolution, was marked by significant technological advancements and changes in the way goods were produced.
Prior to the introduction of machines, most goods were produced by hand, which was time-consuming and limited the number of goods that could be produced. With the introduction of machines, production increased significantly, leading to increased productivity and economic growth. However, the early era of using machines was also marked by several challenges some of which include.
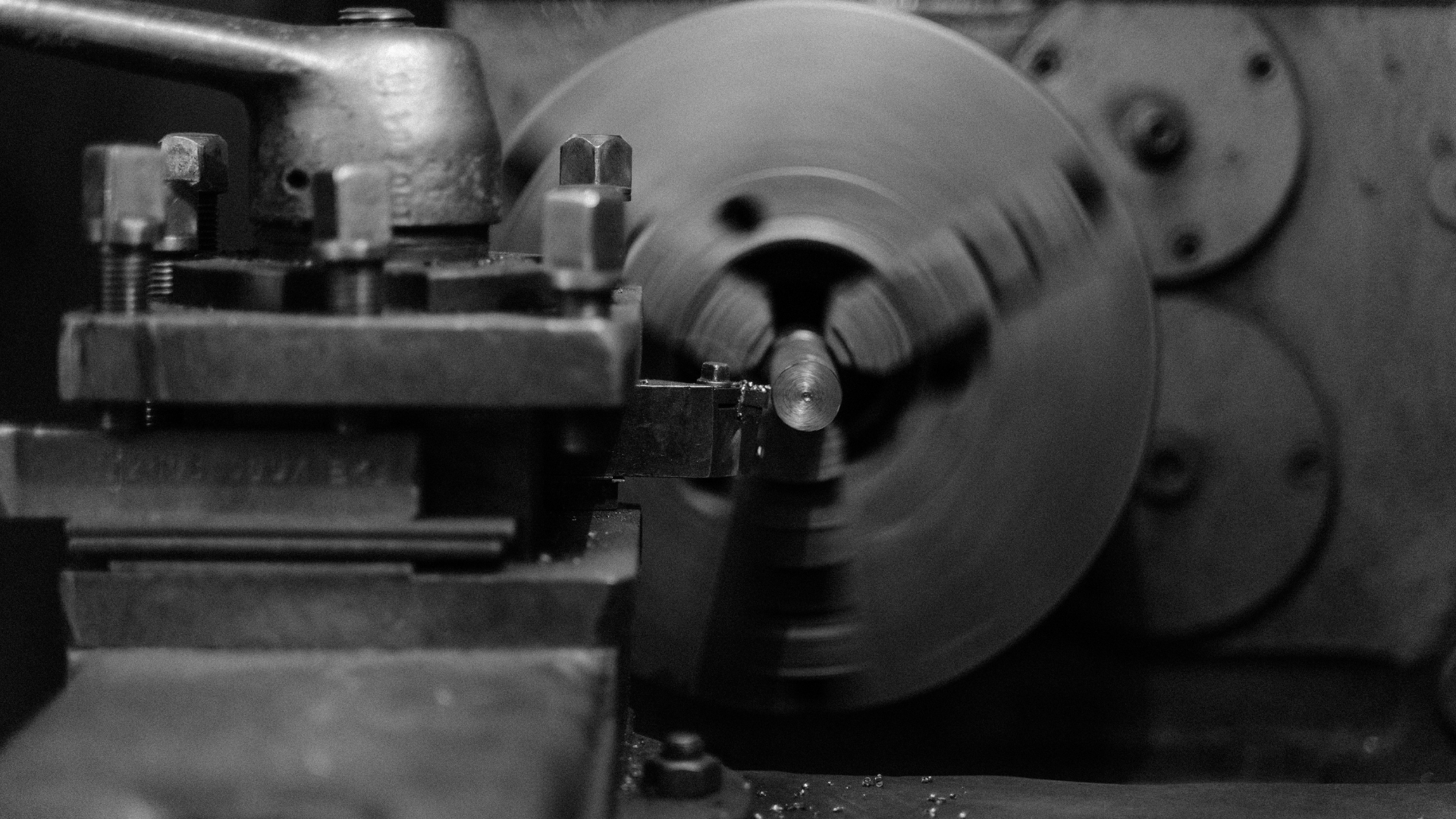
Problem of Safety & Training
In the past, machines were often handled without proper safety and training, which led to many accidents and injuries. Workers were expected to learn on the job, and there were no standardized training programs to ensure they knew how to operate machinery safely.
Without proper training, workers often do not understand the hazards associated with operating machinery, such as the risk of entanglement in moving parts or the dangers of chemicals used in the manufacturing process. This lack of understanding led to many accidents and injuries.
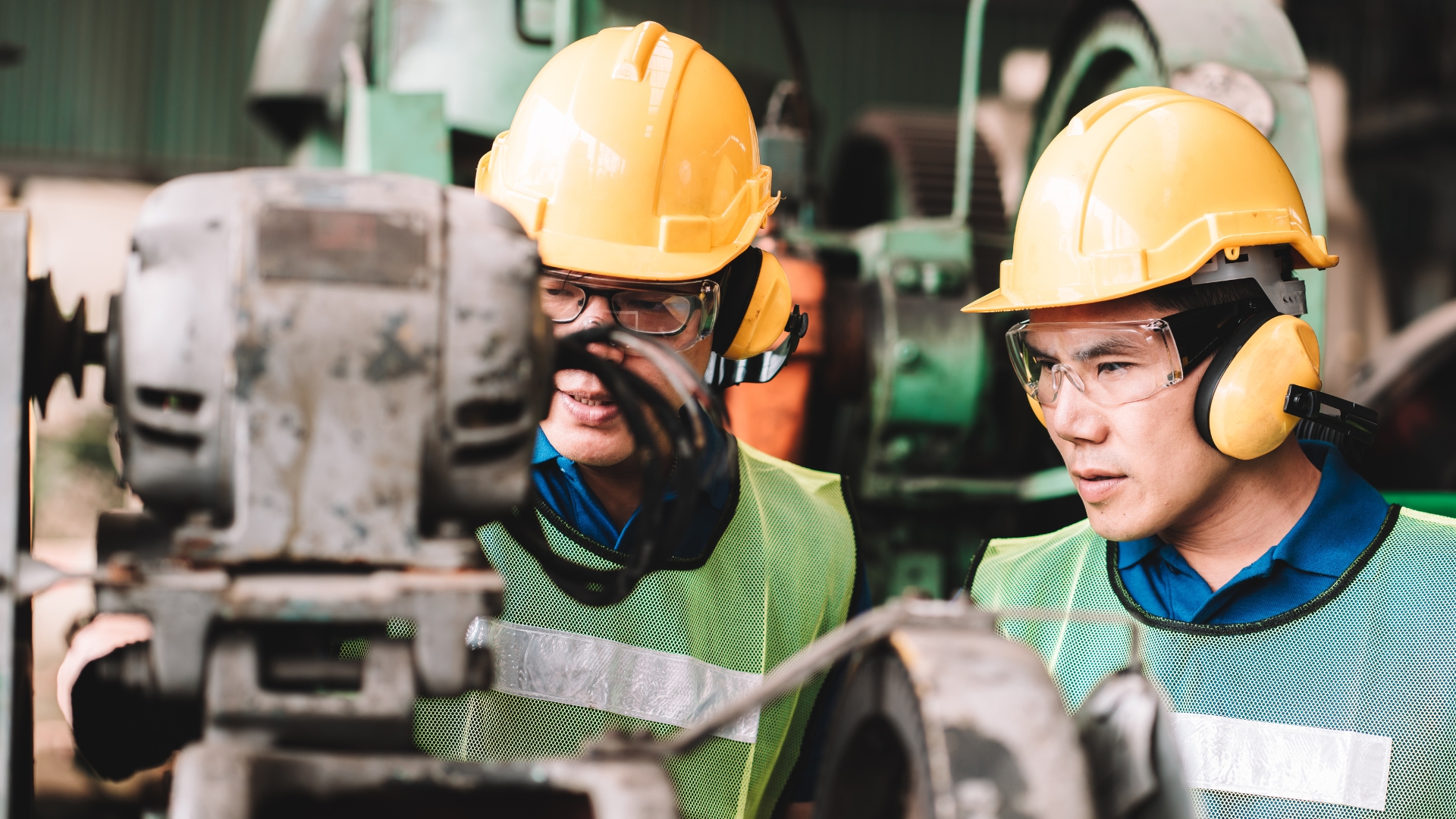
Furthermore, workers did not have access to the protective equipment necessary to operate machinery safely. For example, they did not wear gloves or goggles, which left them vulnerable to injuries from flying debris or harmful chemicals. This lack of protective gear meant that accidents and injuries were more likely to occur.
When accidents did happen, there was often no clear protocol in place for dealing with the aftermath. In many cases, injured workers received little to no compensation or support from their employers. As a result, workers were reluctant to report accidents or injuries, which led to further dangers in the workplace. The handling of machines without proper safety and training in the past was a dangerous and often deadly practice.
It was only with the development of standardized safety regulations and training programs that these risks began to be addressed, making workplaces safer and reducing the incidence of accidents and injuries.
While operating machines such as lathe, the safety measures for lathe machines were not adequate in the past, and workers were often injured due to entanglement with the rotating parts or from flying debris. It was only with the development of safety regulations and training programs that these risks began to be addressed, making workplaces safer and reducing the incidence of accidents and injuries.
Development Of Safety Devices and Safety training
Automatic machinery can be as basic as a pneumatic cylinder or as complex as a group of interconnected automation components. No matter how complicated the system is, the operator, integrator, or maintenance personnel's safety must be taken into consideration.
Depending on the system they are implemented in, safety systems can be either very straightforward or quite complex. The complexity of the safety system will often increase with the complexity of the automated system. Making a choice on which safety equipment to use and when can be difficult because there are so many different options available.
It is important to understand these safety devices and how they work to ensure that workers can operate machinery safely. Employers must provide proper training on these devices and ensure that workers are aware of the risks associated with operating machinery. Workers must also be encouraged to report any safety concerns or issues immediately to prevent accidents or injuries from occurring.
In earlier days, safety training was often non-existent or inadequate which would result in injuries and fatalities. Over time, as awareness of workplace safety grew, employers began to implement safety training programs. These programs were typically conducted in person, often by supervisors or safety officers. Training sessions might include lectures, demonstrations, and hands-on exercises.
As technology advanced, safety training evolved as well. Training programs became more specialized, and the development of new technologies in the area of safety began to rise as a result VR safety training programs and tools started to be built.
The development of VR safety training for operating lathes was driven by the need to provide a safe and effective way for workers to learn how to operate lathe machines without risking injury or damage to equipment.
With the development of VR technology, it became possible to create realistic simulations of lathe operations that allow workers to learn and practice in a safe and controlled environment. VR safety training allows workers to experience and respond to various scenarios that could potentially be hazardous in the real world, without putting themselves or others at risk
For instance, take the example of operating a lathe machine. Many safety devices have been developed in recent times some of which include:
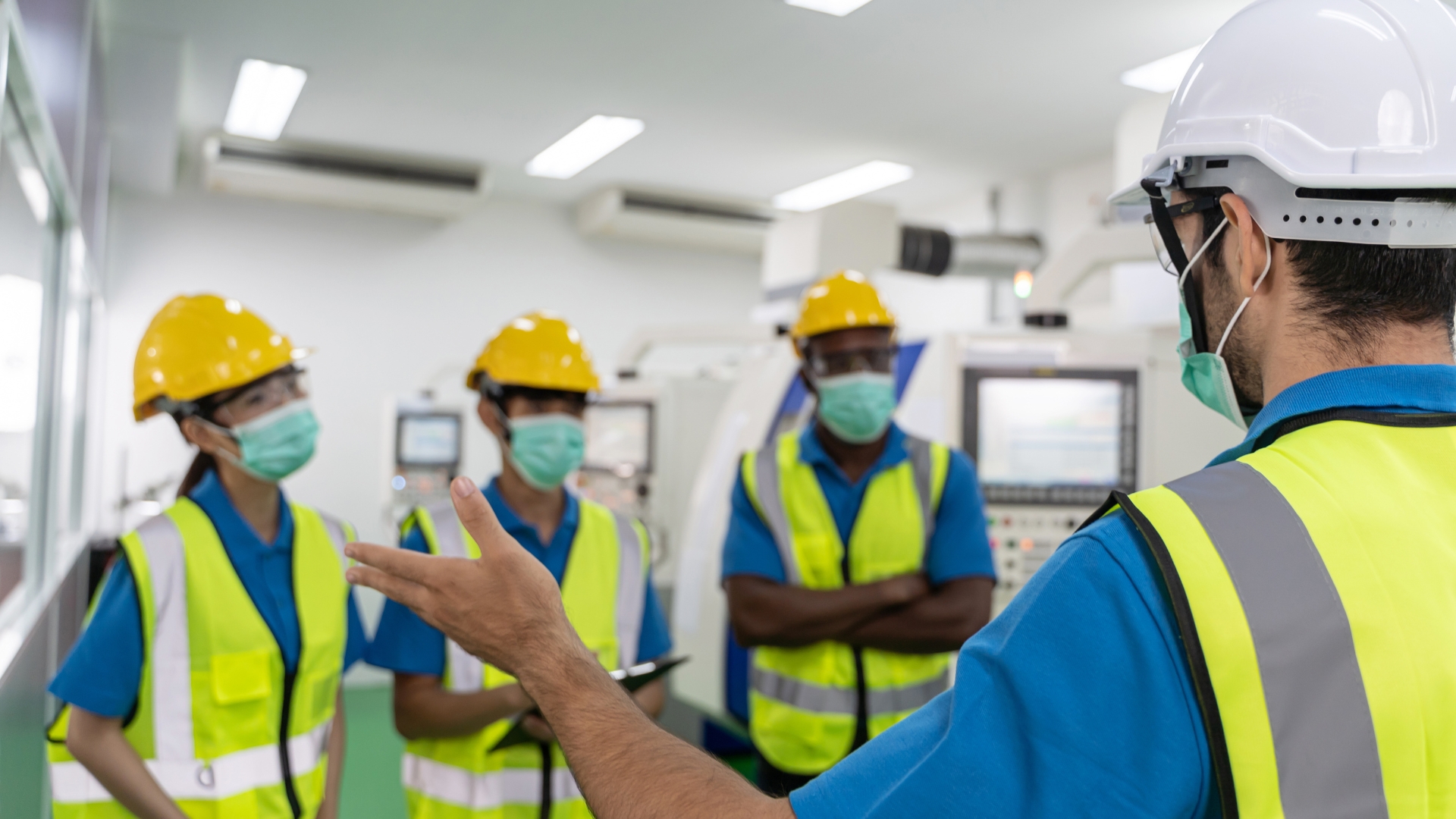
Understanding VR-Based Training
Virtual reality (VR) technology is becoming increasingly popular in industrial training, including lathe tool training. VR-based training for lathe tools involves using a computer-generated environment to simulate real-world lathe operations, allowing trainees to practice and develop their lathe tool skills in a safe and controlled environment.
One of the key advantages of VR-based training for lathe tools is that it offers a more immersive and effective learning experience. Trainees can practice lathe tool operations in a virtual environment that closely mimics the real world, allowing them to gain practical experience without the risk of injury or damage to equipment. The interactive and immersive nature of VR technology also makes training more engaging and enjoyable, which can help to improve knowledge retention and motivation.
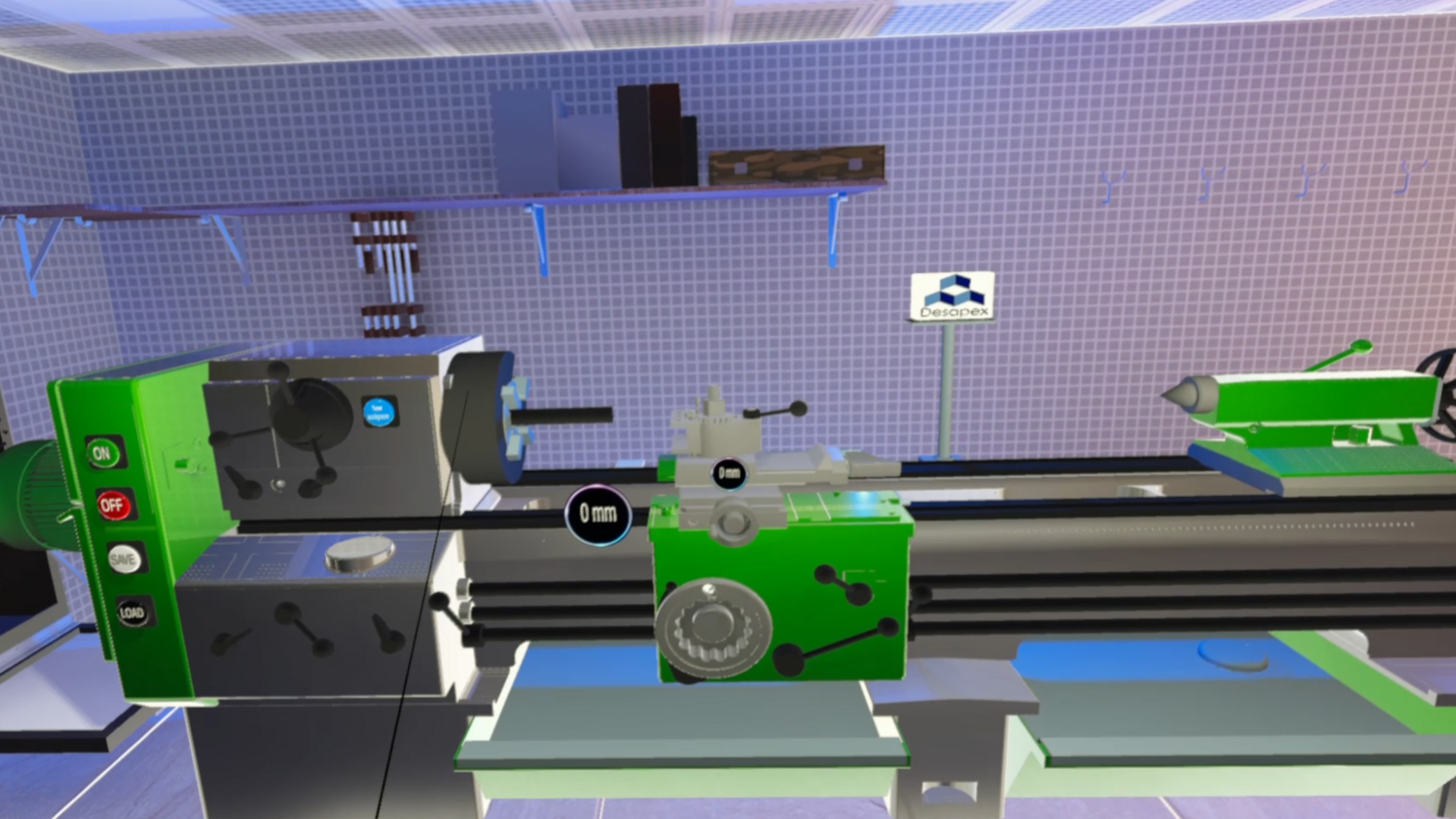
Another benefit of VR-based training for lathe tools is that it allows for customized and targeted training. Trainees can select specific lathe tool operations to practice and receive feedback on their performance in real time. This allows for more personalized training that can be tailored to the individual needs and skill level of each trainee. VR-based training for lathe tools can also save time and resources. Traditional lathe tool training often requires trainees to have access to expensive and complex equipment, as well as specialized trainers. VR-based training can be conducted from any location with a VR headset and a computer, making it more accessible and cost-effective.
Steps Involved In Training In Detail
There are several steps involved in VR-based training some of them include:
Virtual Environment Exploration
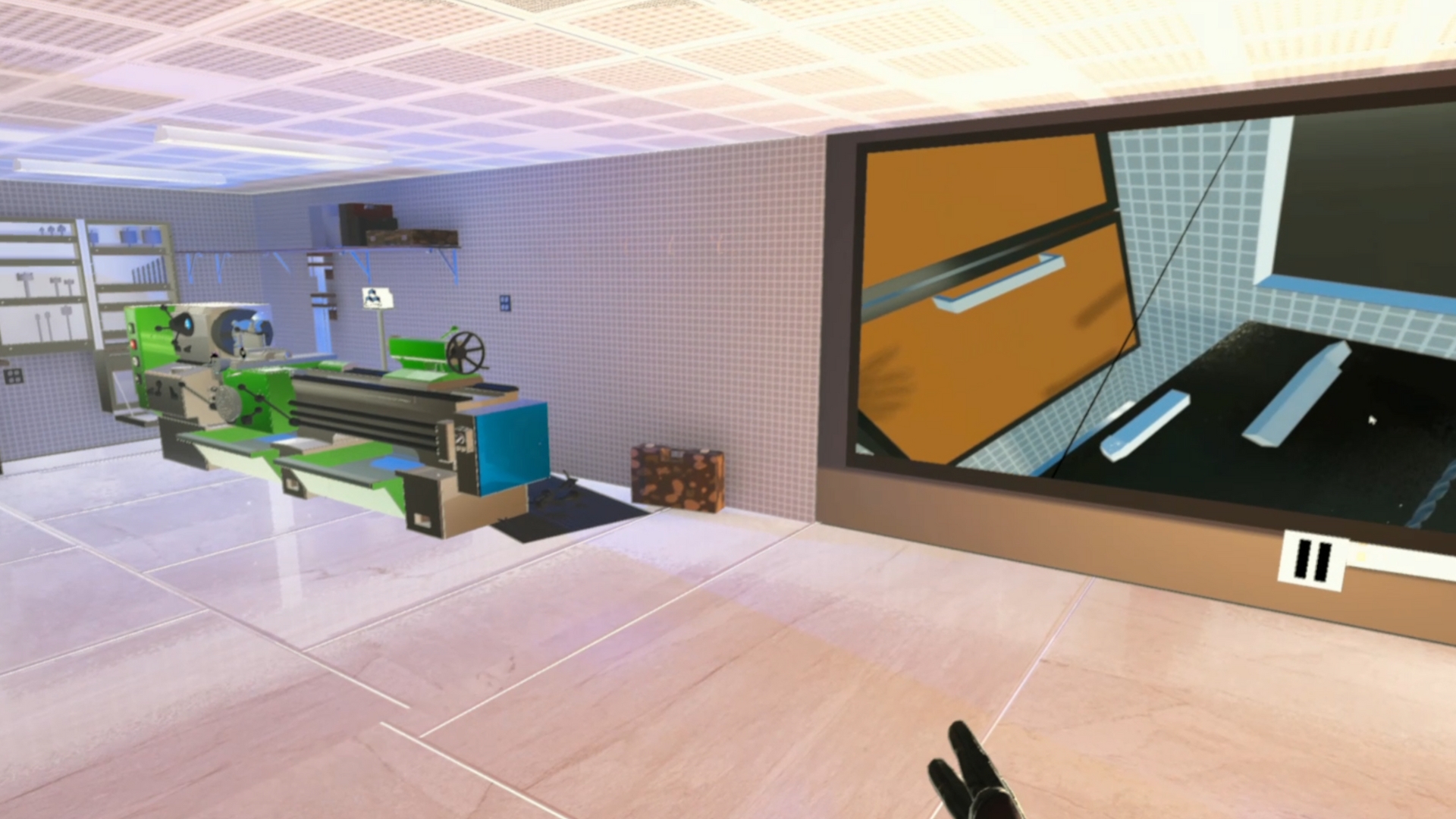
In VR, users can move through these environments and interact with objects and other elements within them, creating a sense of presence and immersion in a virtual world. This can be used for a variety of applications, such as gaming, training, education, etc.
Virtual environment exploration in VR can be accomplished through various means, including using handheld controllers to move and interact with objects, using natural body movements to control movement and interactions, or a combination of both. Additionally, some VR systems may incorporate haptic feedback or other sensory cues to enhance the sense of immersion and presence in the virtual environment.VR provides a way of interacting with things which gives users a realistic experience of the virtual world captured in a Virtual environment.
In our use case, the VR haptic feedback is triggered when a rule is broken and the Environment has fully immersive music making it more and more realistic to the trainee using the VR Training.
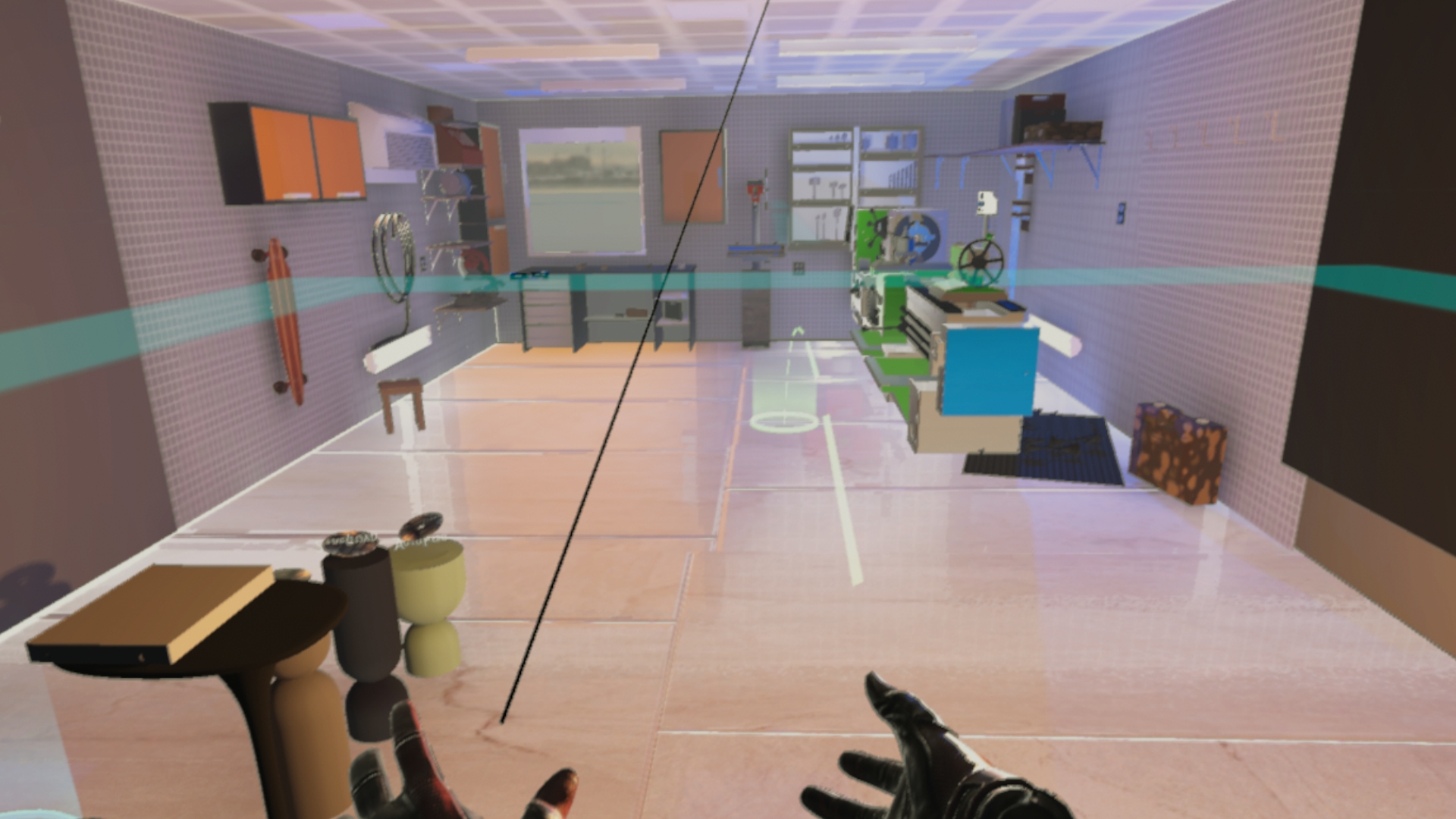
Identification Of Lathe Parts In Detail
The trainee who is supposed to undergo VR-based equipment training needs to understand and identify the parts of the lathe machine which is first and foremost understanding and VR gives an efficient and descriptive platform to view the lathe parts in 360 degrees.
The trainee can easily view any part such as the Headstock, Tailstock, Toolpost, Chuck, Spindle, etc with just one touch to the part in VR. Through this one can easily get the part details and information regarding how to use and handle the part effectively. And also an exploded view of Parts helps users understand how each component works.
VR technology allows us to interact with the virtual environment through its interactive features. Using these features to rotate and zoom in on the lathe model, allows us to get a better look at each component and its position on the machine.
By utilizing labels and annotations, VR training programs offer the ability to label and annotate the different components of the lathe. Using these tools to identify each part and learn about its function is a good way to become familiar with the lathe parts.
To really master identifying lathe parts in VR lathe training, we need to review and repeat what we have learned. Take the time to review the different parts of the lathe model regularly, and practice using the machine until we feel comfortable identifying each component and using them properly.
Knowing the part details in VR lathe training, can save expenses to a larger extent as a new user operating a lathe can make several mistakes while operating and in some cases might damage certain lathe parts that are very expensive and can become problematic to the user, machine, and Enterprise. Therefore VR based lathe training is the best method as the user can test his operating skills figure out his mistakes and learn from them conveniently.
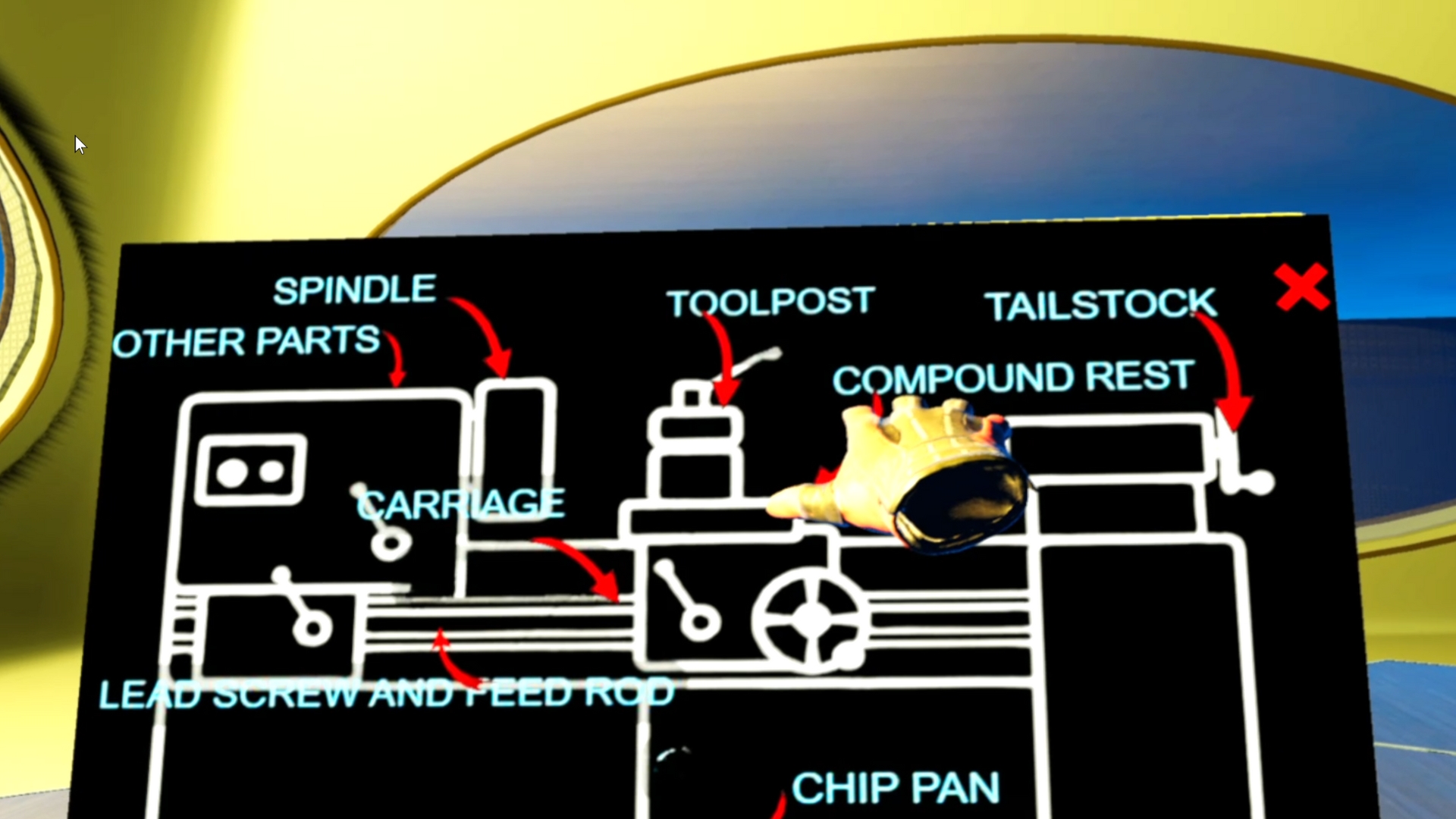
Identification Of Safety Gear In Detail
Safety gear is crucial when it comes to operating a lathe machine, as it helps prevent accidents and injuries. A lathe machine is a powerful tool used for cutting, drilling, and shaping materials, and it can be dangerous if not handled properly. Therefore, wearing appropriate safety gear is essential to ensure the operator's safety.
VR lathe training can give information to the user about what safety gear needs to be worn during lathe operation in several ways:
To give information about safety procedures while operating lathe machines, VR lathe training is the best solution as the user can test his skills on the workpiece and with full safety equipment loaded and one can observe and know the amount of risks included while doing a lathe operation through hands and can get a clear picture of what safety measures need to be taken while operating the lathe machine.While also gaining confidence to use the equipment and improving skills daily.
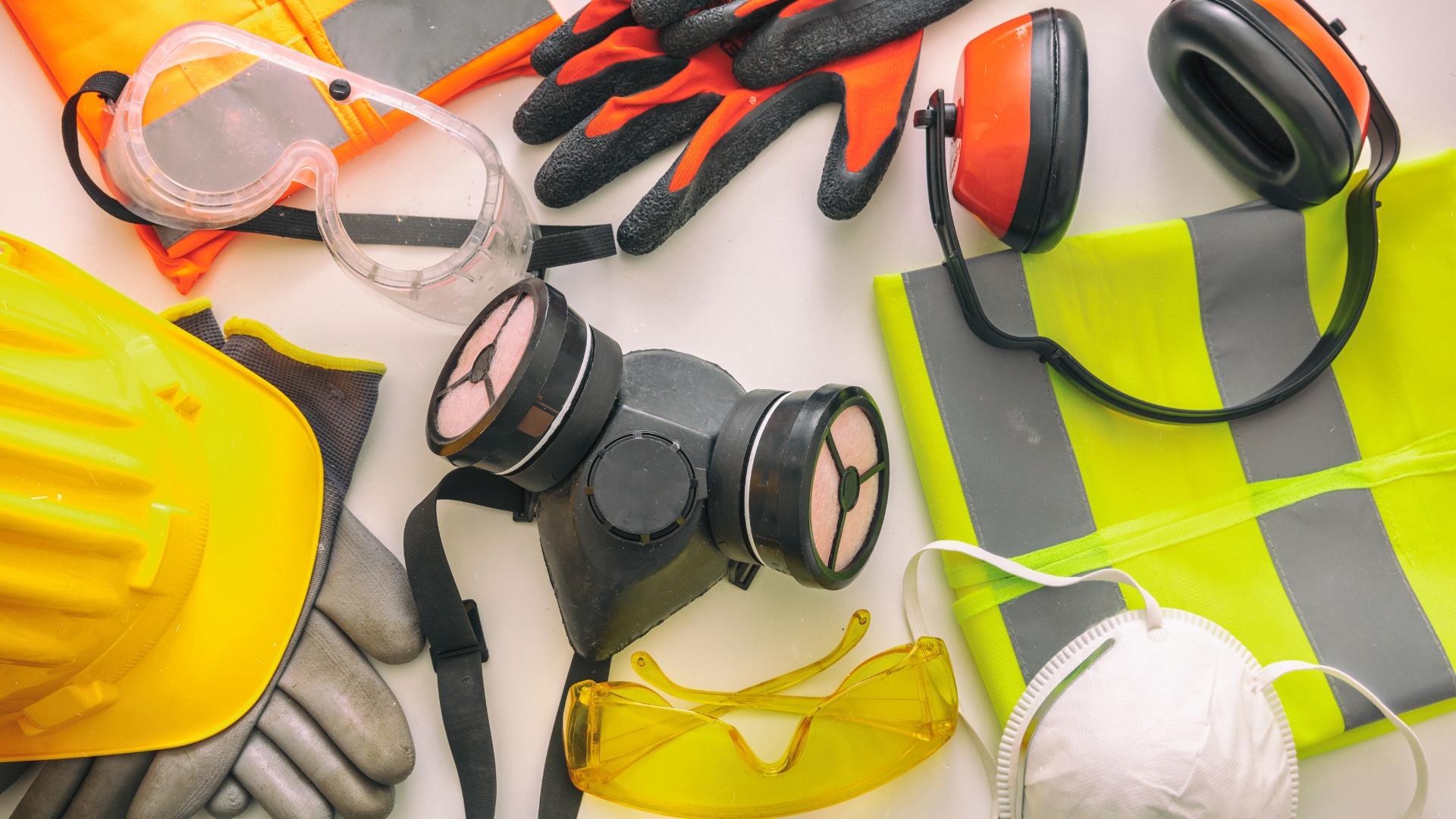
Identification Of Type Of Tools And Their Usage
A lathe is a machine tool used for shaping and cutting various types of materials such as wood, metal, and plastic. It works by rotating the workpiece while a cutting tool moves along the material to remove excess material and create a specific shape. In this process, various tools are used to perform different operations.
Familiarize yourself with different types of lathe tools - Before using the VR-based lathe training tool, you should familiarize yourself with different types of lathe tools. These include turning tools, facing tools, boring tools, threading tools, and parting tools.
Study the VR mode - Take the time to carefully study the VR model of the lathe tool. Start by examining the overall shape and size of the tool, and then zoom in to explore each part in detail.
By providing suitable annotations and animations under VR we can give users the information of the tool that has been picked and how to use the respective tool to test their skills on operating the lathe.
Through VR-based equipment training many types of tools such as cutting, parting, boring, facing, knurling, and threading can be carried out without the risk of damaging or putting effort into lifting heavy and sharp tools which can be dangerous with bare hands. VR gives users the freedom to test any tool multiple times and carry out the lathe operations as many times as they can without the fear of breaking or damaging the tools and workpieces. It can be a game changer as the tools made up of expensive materials such as diamonds can be brought under VR and tested without fear of damaging tools.
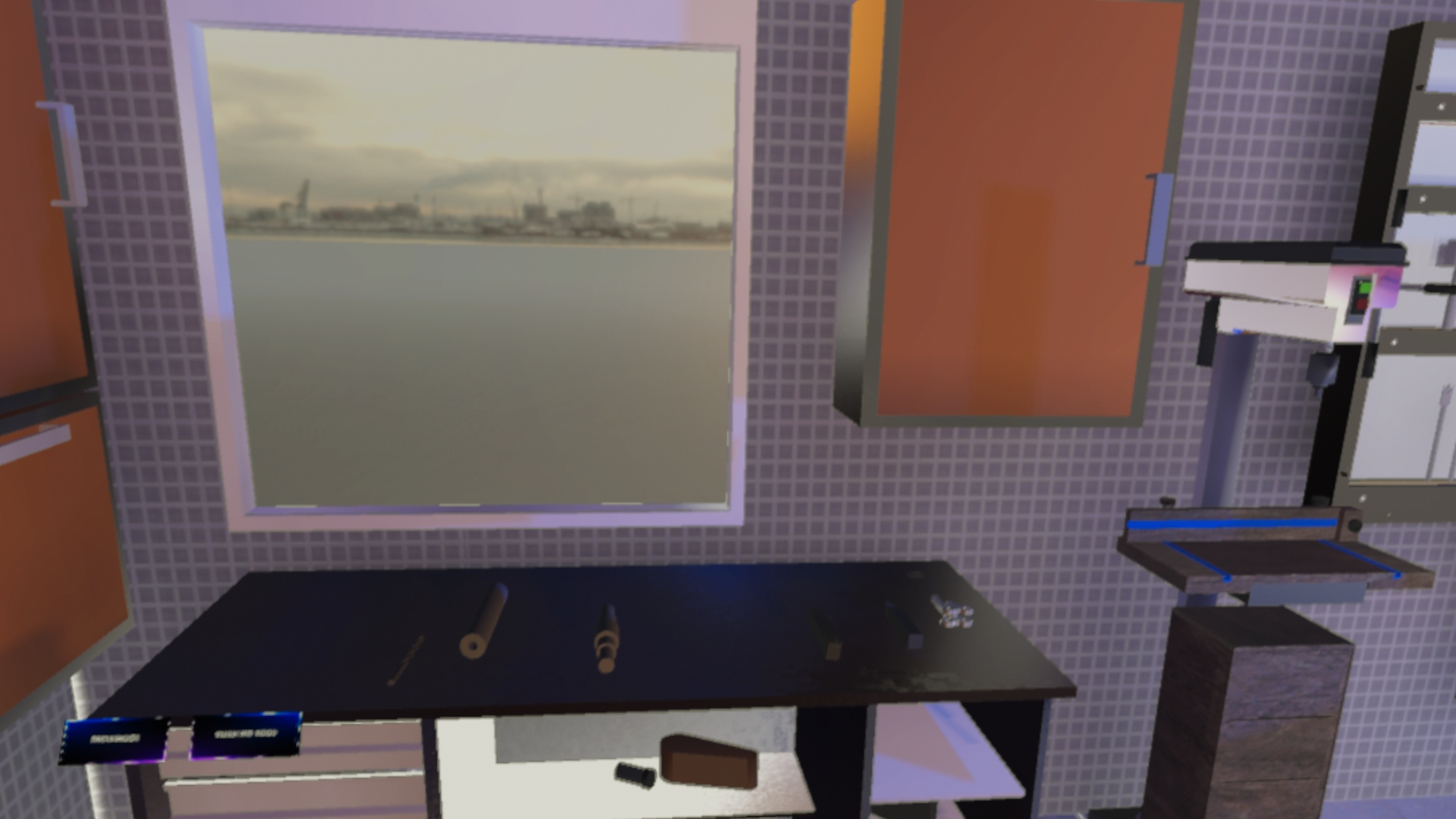
Using Lathe In VR Simulation
Virtual Reality (VR) simulations can be an effective way to help users gain practical experience and feel confident and competent when operating a lathe. Here are some ways in which VR simulations can help:
Lathe machine developed in VR is the best way to demonstrate how a task that could have led to many injuries while training and using can be easily performed and understood even without the presence of a supervisor leading to safety, reduced cost of training students, understanding the concepts in a more immersive way. Through VR many applications can be visualized more dynamically.
Applications of VR simulations are many and are already in use in many industries but are unable to explore their full potential. Increasing the use of VR in simulations in different industries will help in broadening the uses and exploring more about this wonderful and futuristic technology.
Performance Evaluation And Analytics Of User Readiness
Performance evaluation and analytics are essential to assess user readiness in VR-based lathe training. Virtual Reality (VR) technology has proven to be an effective tool for industrial training, and it offers a safe and controlled environment to train users in various industrial applications such as lathe machining.
Performance evaluation is crucial to assess the progress of users in their training program. VR-based training provides an immersive and interactive learning experience that simulates real-world scenarios. With the use of sensors and other tracking devices, VR systems can gather data on the user's performance, including speed, accuracy, and completion time. This information can be used to measure the user's proficiency level, identify areas of improvement, and track progress over time.
Analytics play a critical role in evaluating the effectiveness of VR-based training. By analyzing the data collected during training, it is possible to identify patterns, trends, and areas for improvement.
Analytics can also help trainers understand the learning styles and preferences of individual users, allowing them to tailor the training program to suit their needs.
In VR-based lathe training, performance evaluation and analytics can help identify areas where users may be struggling, such as with specific lathe operations or techniques. This information can then be used to adjust the training program, providing additional support or resources to help users overcome these challenges.
Score Card And Peer Rankings
Scorecards and peer rankings are powerful tools that can help users evaluate their progress and compare their performance to others while using a VR lathe training tool. Here's how these features work -
Scorecards - Scorecards are a way to track and measure a user's progress through a VR lathe training tool. These scorecards may be broken down into different categories, such as accuracy, speed, or safety. As the user completes different training exercises, their scores are recorded and added to their scorecard.
Peer rankings - Peer rankings allow users to compare their performance to other users who have completed the same VR lathe training tool. These rankings may be displayed in a leaderboard or a similar format that shows the top performers. Users can see how they stack up against their peers and use this information to motivate themselves to improve.
Together, scorecards and peer rankings provide users with valuable feedback on their progress and performance. By tracking their scores and comparing themselves to others, users can identify areas where they need to improve and set goals to work towards. This feedback can also help users stay engaged and motivated throughout the training process.
For example, a user may notice that their accuracy score is lower than other users in their peer group. They can then focus on improving their accuracy by practicing specific lathe techniques or reviewing safety guidelines. As they work to improve, they can see their score increase and move up in the peer rankings, which can provide a sense of achievement and satisfaction and also reach a person of higher rank to improve himself and learn new techniques.
Conclusion
Proper training is crucial when using lathe machinery because it helps ensure the safety of the operator and improves the quality of the work produced. Lathe machines are powerful and can be dangerous if not used correctly, making it essential that operators receive adequate training on how to use them safely and effectively.
One way to provide effective training is through the use of virtual reality (VR) technology. VR-based lathe training can provide numerous benefits over traditional training methods, such as:
Overall, proper training when using lathe machinery is essential to ensure the safety of the operator and the quality of the work produced. VR-based lathe training offers numerous benefits over traditional training methods, making it an effective and efficient way to train operators.
Comments
Post a Comment